新闻动态
- 树脂砂轮片
- 钢丝轮系列
- 刷系列
-
炉通扫系列
- 砂布轮系列
- 砂布页轮系列
- 砂纸、砂布、砂带系列
- 抛光盘系列
-
海绵抛光系列
- 金刚石系列
- 玻璃抛光系列
-
黑金刚系列
- 磨头系列
-
旋转锉系列
-
陶瓷砂轮
- 研磨膏、抛光腊系列
-
油石系列
- 百洁布、无纺布系列
-
羊毛抛光系列
- 布轮、麻轮系列
-
拉丝轮系列
-
尼龙轮系列
-
电动工具
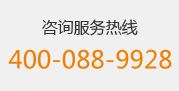
利用金刚石补强材料改善碳化硅陶瓷的断裂韧性研究
发布时间:2017-03-31 11:05:29
摘要:
碳化硅作为一种硬质高强度材料,广泛应用于磨料、转盘、轴承和高温涂层等工程技术设备等领域。由脆性特质引起的较差的断裂韧性是碳化硅的一个技术制约。近年来,有研究人员研发制备出纳米金刚石(ND)颗粒增强型碳化硅材料,既改善了断裂韧性又不影响材料本身的强度。本论文利用分子动力学模拟对新型碳化硅131材料中纳米金刚石和纳米硅颗粒的补强效果进行了研究。实验选取两种类型的纳米颗粒:(a)裂缝尖端前面成簇的颗粒;(b)分布一致的颗粒。对模型I和模型II的断裂韧性进行测量。实验观察得知,碳化硅中添加纳米金刚石能100%程度地改善模型II断裂韧性,25%程度地改善模型I的断裂韧性。
引言
碳化硅作为一种硬质高强度材料,广泛应用于磨料、转盘、轴承和高温涂层等工程技术设备等领域。但和多数陶瓷材料类似,碳化硅有~9GPa的高抗屈强度、~2800kg/mm2的高硬度和~4.6MPa.m0.5的低韧性。牢固的共价键和离子键所形成的微结构造成了碳化硅的这种特殊属性;而较低的韧性则大大制约了碳化硅在诸多领域的应用。一般情况下,韧性属性包括强度和变形性。强度高变形性低的材料整体上都有较低的韧性。增强材料韧性一般有两种方法:利用外部机制和利用内部机制。对于陶瓷材料的增韧则主要是利用外部机理;常见方法有:(1)延性定相。通过大规模延性相变形在断裂尖端周围应变松弛,或者在断裂尖端背面利用延性相伸展来进行裂纹钝化、裂纹搭桥,从而抵制裂纹发生和扩散。(2)粒化。在晶粒间界处增韧以减少裂纹密度。(3)通过多层化来增强薄膜和衬底间的粘合。(4)纳米纤维增强。在纤维-基体界面处使裂纹发生偏离。(5)金刚石烧结等对裂纹进行搭桥。
结构的分子建模
图一(a)为碳化硅分子模型。
碳化硅作为一种硬质高强度材料,广泛应用于磨料、转盘、轴承和高温涂层等工程技术设备等领域。由脆性特质引起的较差的断裂韧性是碳化硅的一个技术制约。近年来,有研究人员研发制备出纳米金刚石(ND)颗粒增强型碳化硅材料,既改善了断裂韧性又不影响材料本身的强度。本论文利用分子动力学模拟对新型碳化硅131材料中纳米金刚石和纳米硅颗粒的补强效果进行了研究。实验选取两种类型的纳米颗粒:(a)裂缝尖端前面成簇的颗粒;(b)分布一致的颗粒。对模型I和模型II的断裂韧性进行测量。实验观察得知,碳化硅中添加纳米金刚石能100%程度地改善模型II断裂韧性,25%程度地改善模型I的断裂韧性。
引言
碳化硅作为一种硬质高强度材料,广泛应用于磨料、转盘、轴承和高温涂层等工程技术设备等领域。但和多数陶瓷材料类似,碳化硅有~9GPa的高抗屈强度、~2800kg/mm2的高硬度和~4.6MPa.m0.5的低韧性。牢固的共价键和离子键所形成的微结构造成了碳化硅的这种特殊属性;而较低的韧性则大大制约了碳化硅在诸多领域的应用。一般情况下,韧性属性包括强度和变形性。强度高变形性低的材料整体上都有较低的韧性。增强材料韧性一般有两种方法:利用外部机制和利用内部机制。对于陶瓷材料的增韧则主要是利用外部机理;常见方法有:(1)延性定相。通过大规模延性相变形在断裂尖端周围应变松弛,或者在断裂尖端背面利用延性相伸展来进行裂纹钝化、裂纹搭桥,从而抵制裂纹发生和扩散。(2)粒化。在晶粒间界处增韧以减少裂纹密度。(3)通过多层化来增强薄膜和衬底间的粘合。(4)纳米纤维增强。在纤维-基体界面处使裂纹发生偏离。(5)金刚石烧结等对裂纹进行搭桥。
结构的分子建模
图一(a)为碳化硅分子模型。
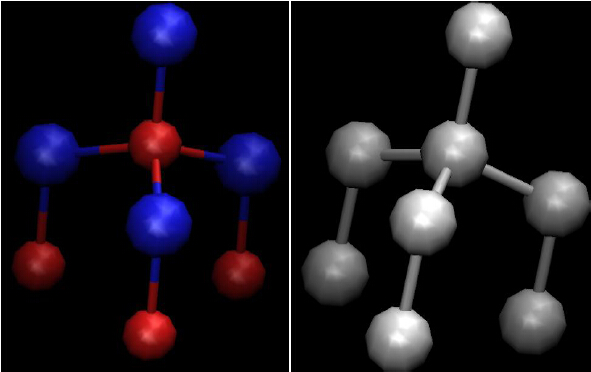
图一:a)纯碳化硅结构(蓝色为硅;红色为碳);b)纯纳米金刚石结构
纯碳化硅模型包括68832个院子。在 WNC模型中将原子从晶体中移除便得到一个中心裂纹长度a=2.62nm,以类似此方法建立若干个纳米复合材料模型。模型1中,碳化硅基体掺入8个固态纳米金刚石颗粒。模型2中,碳化硅基体掺入两个簇丛纳米金刚石颗粒,每个簇丛包含4个纳米金刚石颗粒。模型3中,用洞孔纳米金刚石颗粒替代固态纳米金刚石颗粒。模型4中,ND颗粒建模为不可变形的颗粒。此外,还建立了一个模型,用硅颗粒替代ND颗粒。每个颗粒的形状假定为方形,ND颗粒边长为0.357nm,碳化硅颗粒边长为0.43597nm。所有模型的原子间交互作用建立在Tersoff potential基础上。
图二:a)有裂缝的纯碳化硅;b)ND增强型碳化硅切片图;c)洞孔ND增强型碳化硅切片图;d)ND分散一致的增强型碳化硅切片图
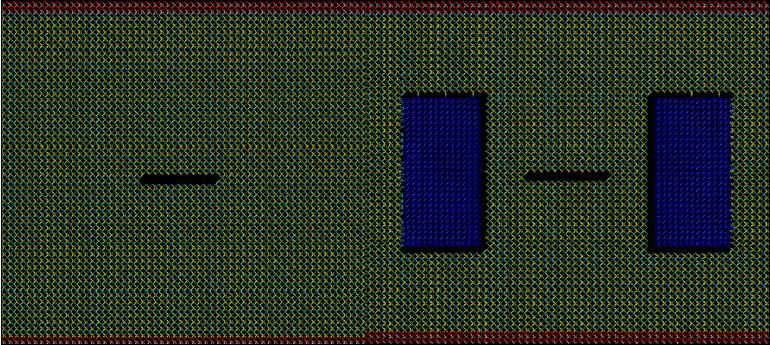
形变的分子模拟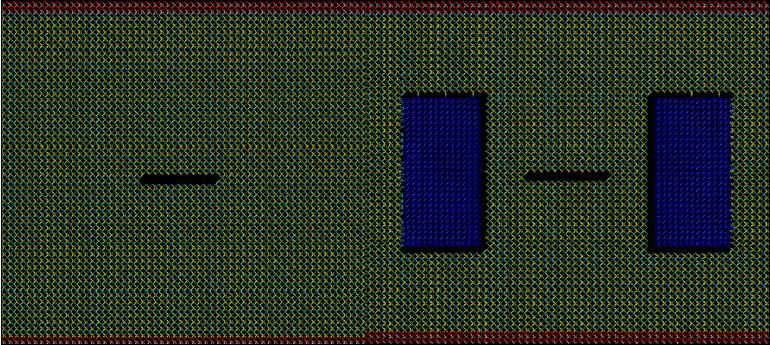

利用Daresbury 实验室开发的2.20版DL-POLY进行所有的模拟实验。实验条件为300k,0.5fs时间步长。实验分两步骤对机械性能进行观察。第一步对原子模型进行平衡,第二步对模型进行渐进轴向机械装载。
平衡状态
将NPT和NVT整体结合,进行平衡状态实验。首先将模型在NPT条件下运行模型,时间步长为30000;然后在NVT条件下对模型进行机械装载。
应力应变曲线
利用应力应变曲线进行抗拉实验和抗剪实验。对所有模型施以应变场,进行轴向拉伸实验。
沿着形变的方向对MD单元的大小进行测量并施以应变,然后对原子的新坐标重新测量以便匹配新的大小。完成初始形变以后,继续对MD进行模拟,在新的MD单元大小范围内对原子进行平衡。重复该步骤以实现持续渐进形变。轴向拉伸方向上的应变增量为0.25%。然后,将系统松弛0.1ps,将系统上的应力调和至大于0.1ps。实验采用周期边界条件。
结果和讨论
图三:嵌入纯ND颗粒的应力应变曲线
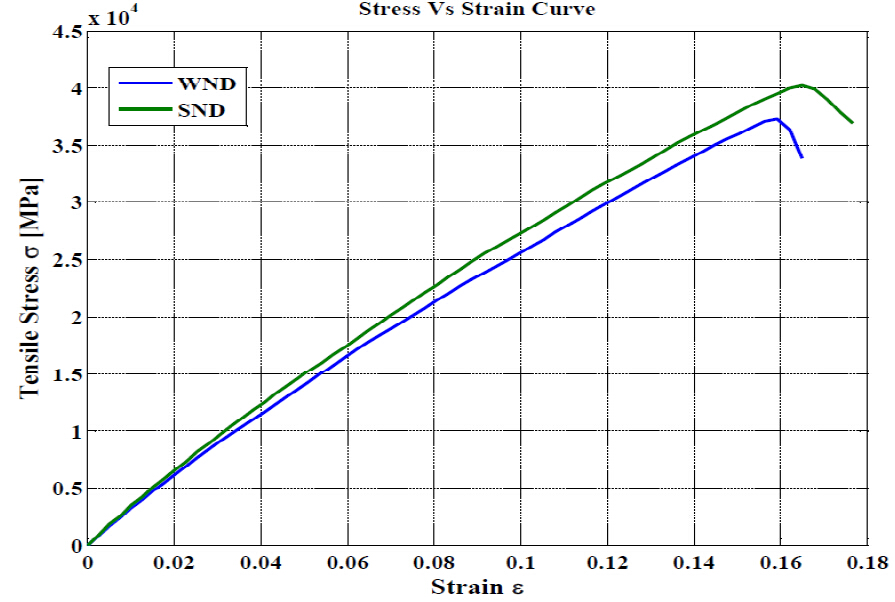
图四:(a)带裂缝的纯碳化硅;b)带裂缝的ND增强型碳化硅
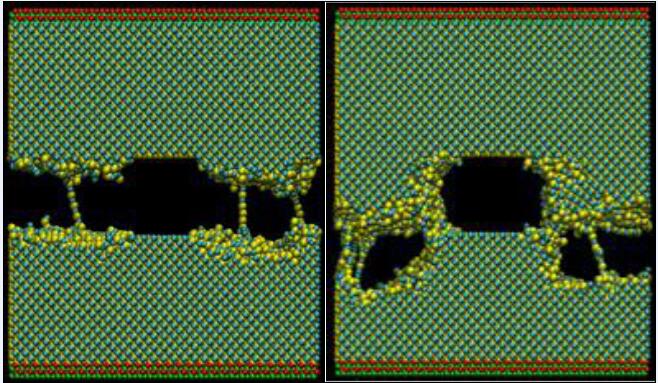
为观察ND颗粒形变性对整体应力应变反应的影响,实验建立了一个ND为不可形变的模拟。曲线如图五所示。图六为对应的MD。可以明显看出不可形变的ND颗粒明显降低了整体强度和韧性。由于ND颗粒是不可形变的,当裂缝产生并影响ND-SiC界面时,不存在能量损失。图五可以看出在10%应变处应力应变发生了弯曲。
图五:嵌入纯ND颗粒的应力应变曲线
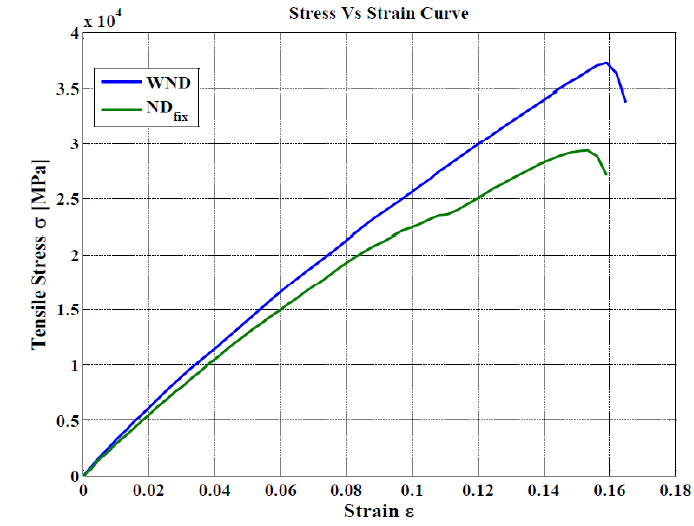
图六:带裂缝的ND增强SiC失败试验品
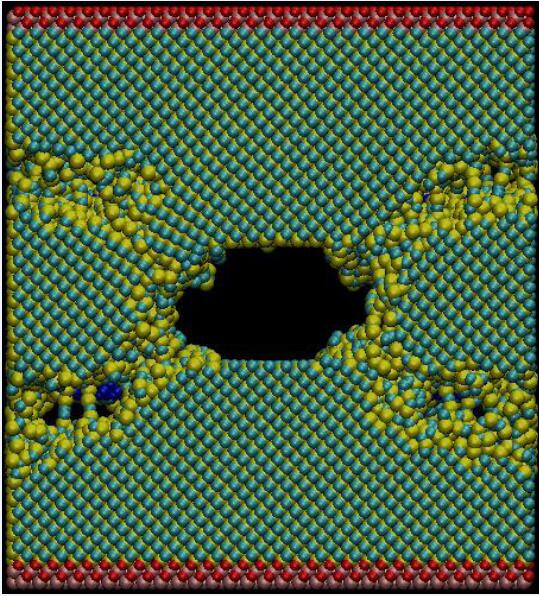
图七:嵌入洞孔ND颗粒的应力应变曲线
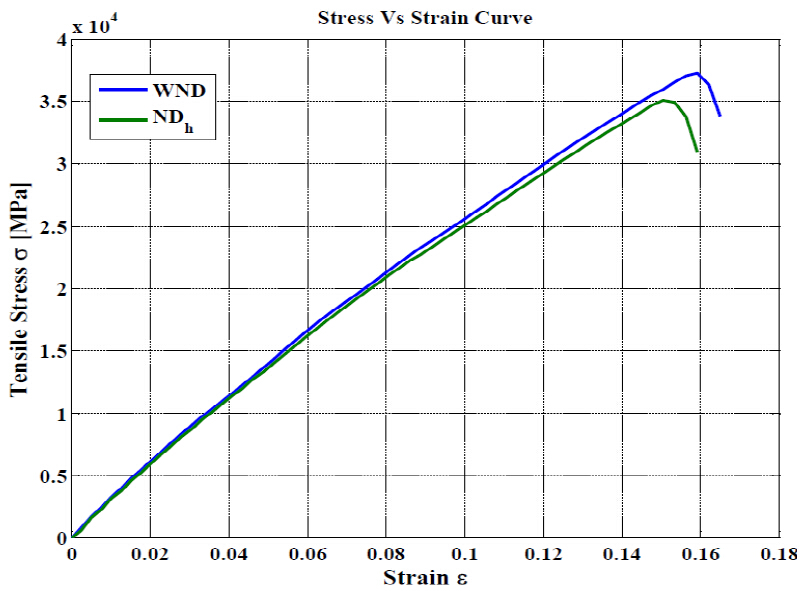
图八:带裂缝的ND增强SiC失败试验品
为完善对纳米颗粒增强效果的评估,实验还进行了不可变形的洞空ND研究,曲线如图九所示。图十为对应的MD。图九可以看出,当不可变形洞空ND嵌入时,整体应力应变性能下降。使用硬质ND时,图十显示类似趋势。这说明和硬质ND增强系统相比,不可变形洞空ND的变形机理是一样的。由此可以推断超硬增强纳米颗粒不会增强其机械性能。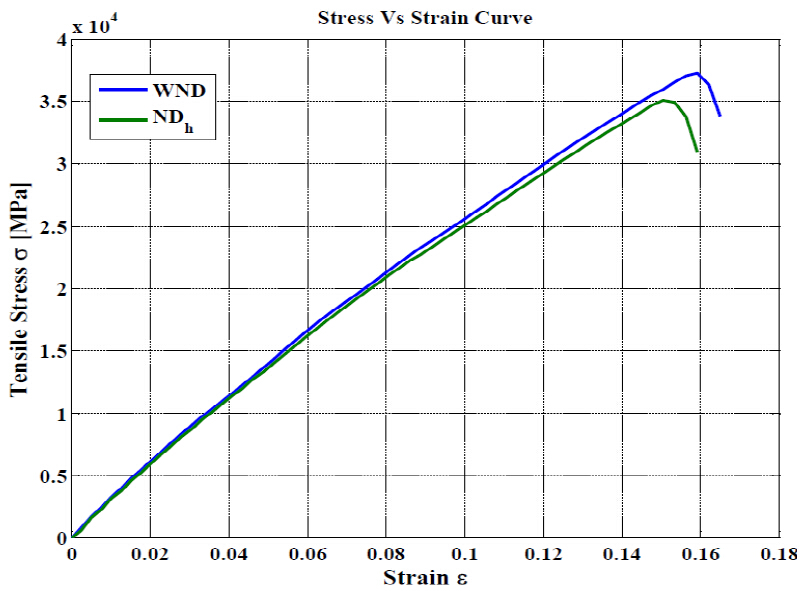
图八:带裂缝的ND增强SiC失败试验品
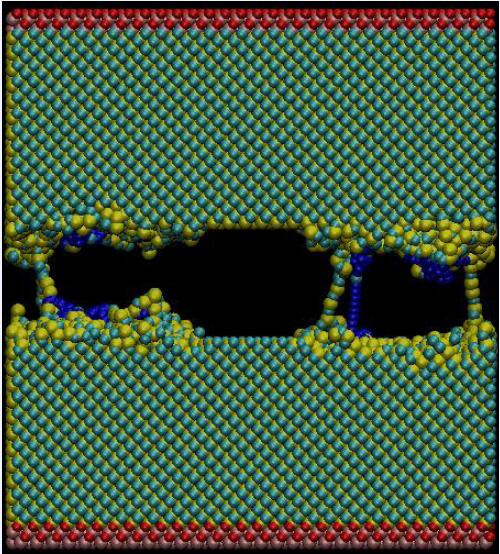
图九:嵌入洞空ND的应力应变曲线
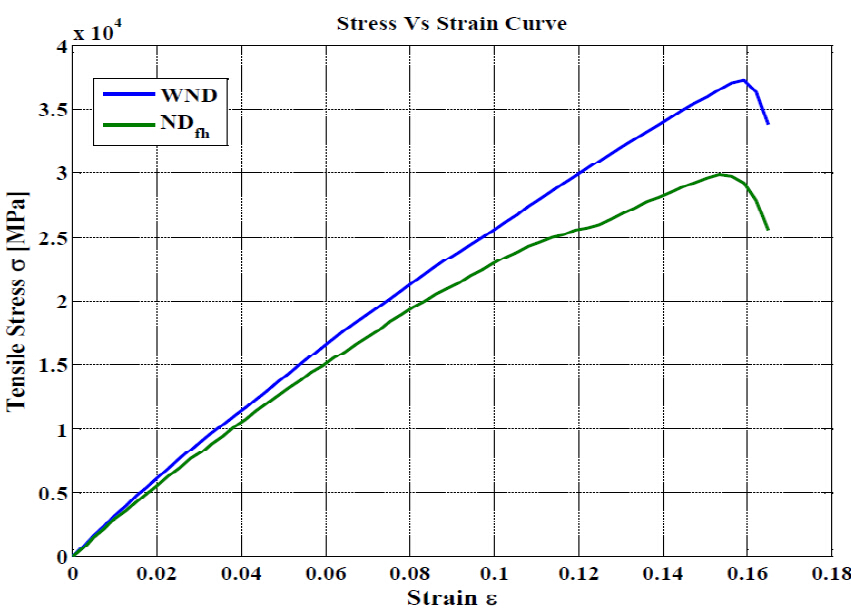
图十:带裂缝的硬质ND增强SiC失败试验品
为研究纳米颗粒属性对SiC基体的影响,实验用同样尺寸的Si替代ND。需要注意的是Si没有SiC更硬,因此把它放入裂缝中。曲线如图11所示。由图可以看出掺入Si增强体后并没有改善整体应力应变性能。
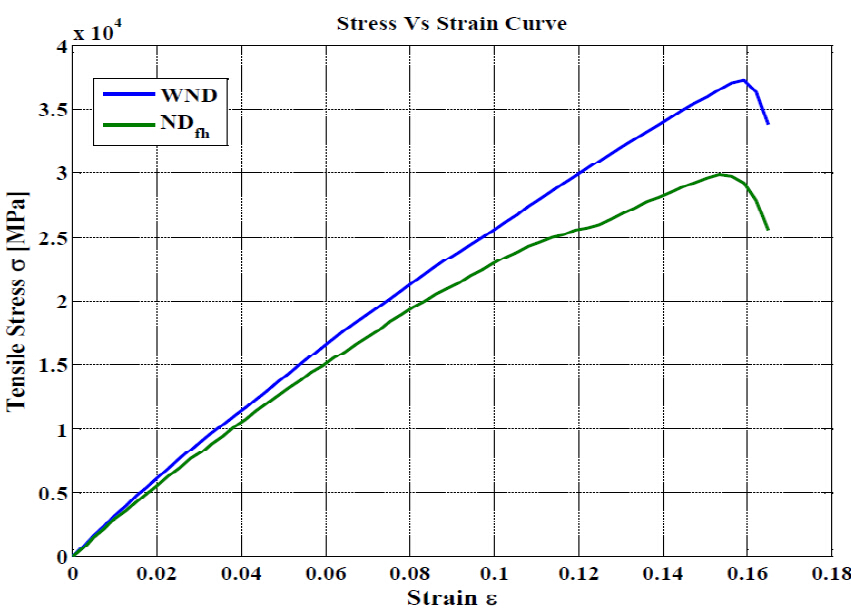
图十:带裂缝的硬质ND增强SiC失败试验品
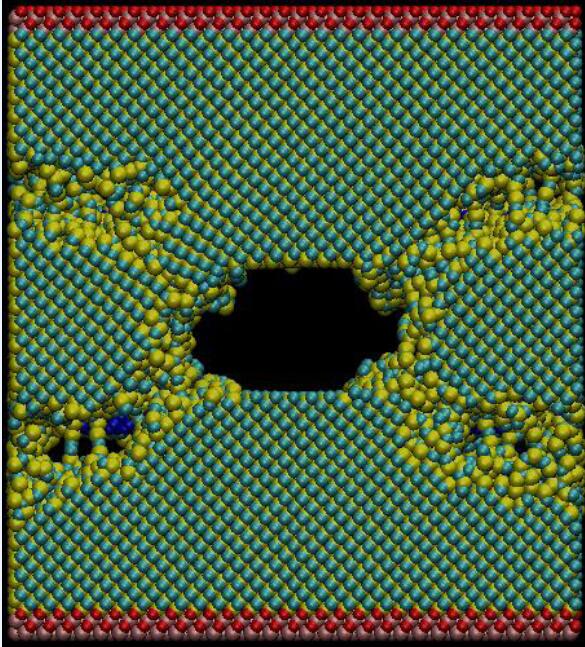
图11:掺入纯Si的应力应变曲线
模型II裂缝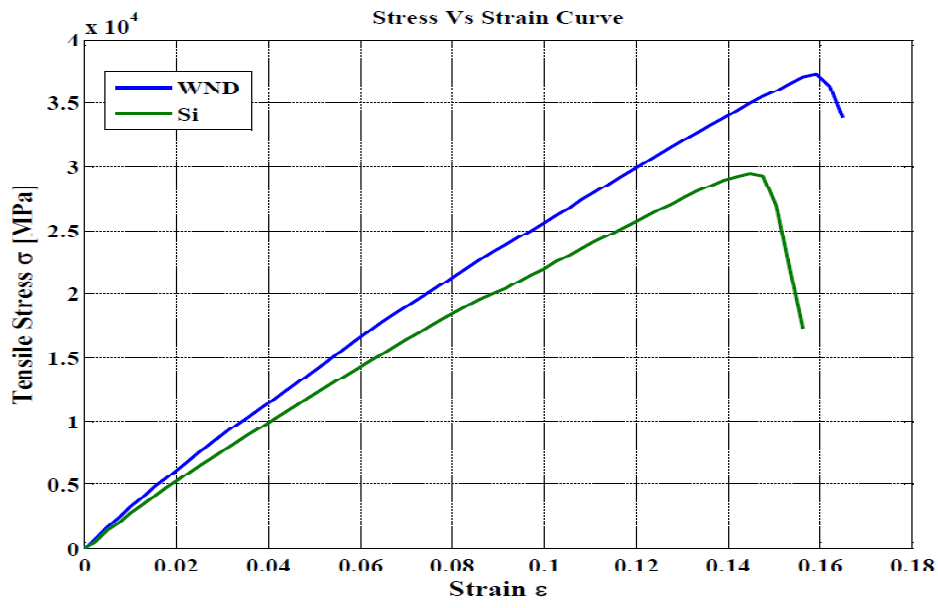
从抗拉实验可以看出SiC的强度和韧性只有在ND颗粒不是超硬属性的情况下才能得到改善。为验证该假设,研究对所有实验进行抗剪实验,结果显示增强ND改善了SiC的韧性。图12为抗剪实验结果。图13为对应的MD。由于错位成核,剪切负载过程中发生显著的塑性变形。
图12:剪切负载的应力应变曲线
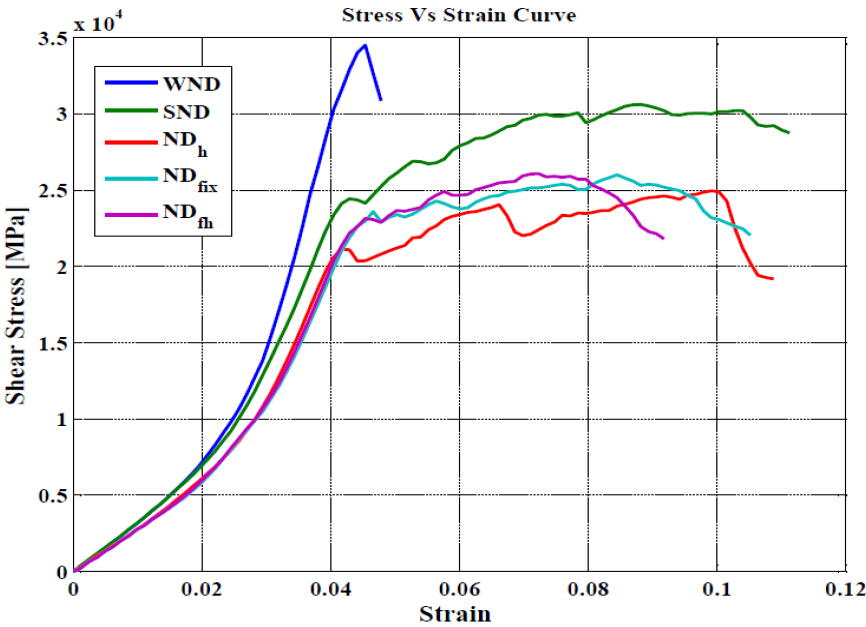
图13:(a)ND-SiC复合材料和(b)纯SiC的剪切试验失败品
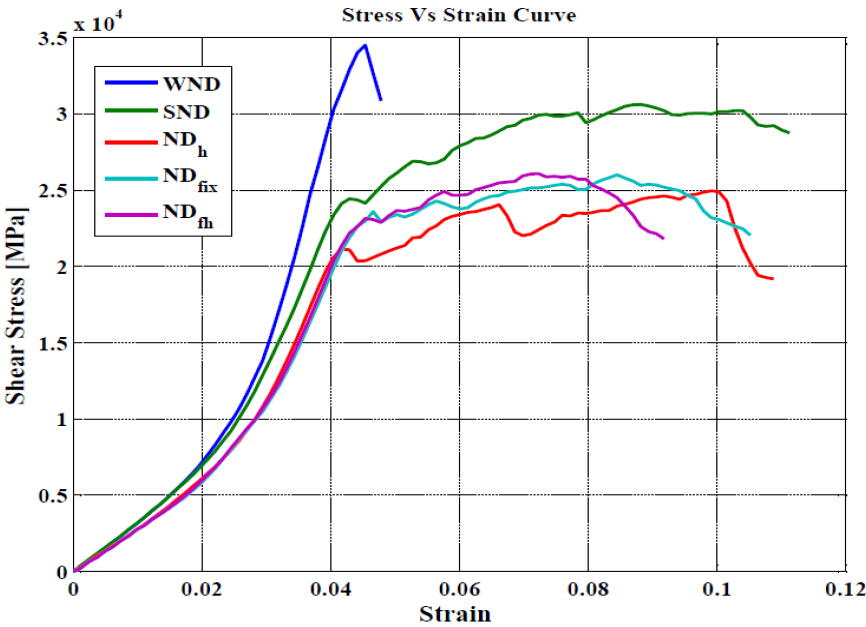
图13:(a)ND-SiC复合材料和(b)纯SiC的剪切试验失败品
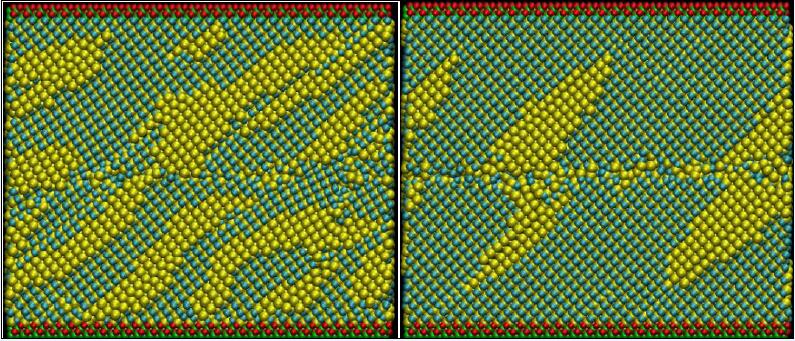